This is one of the most critical functions in profitable product commercialization for regulated industries and global companies that have to comply with a multitude of regulatory agencies.
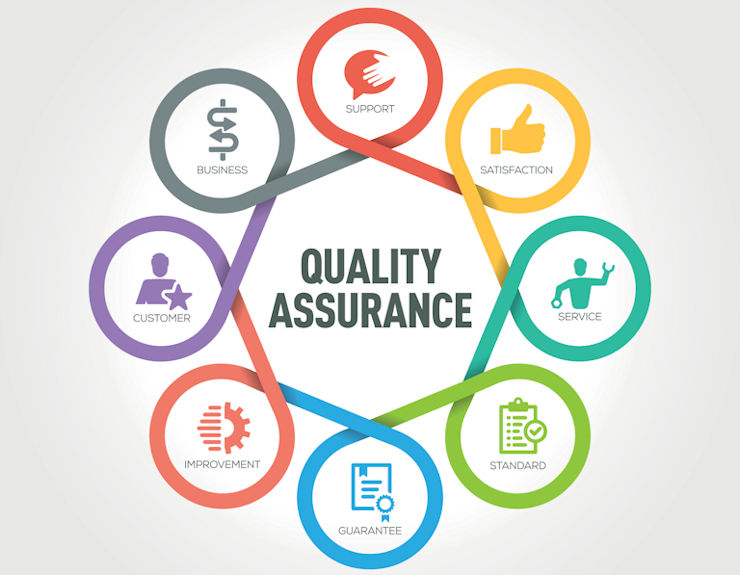
The impact of their activity may directly affect a company’s ability to get a product to market profitably. The time to think about quality and compliance strategies is at the very beginning of the product creation process.
As companies are under pressure to make effective use of capital and be ready for commercialization from the ‘get go’, managing product operations processes including quality and compliance processes becomes a critical element for the overall success of the company. This involves setting up and running effective Design Control, Document Control, ECO processes, and Corrective Action and Compliance Management processes for Product Development and Operations.
In addition, Quality and Regulatory Affairs must support an efficient management of processes that expands beyond the company’s boundaries into the entire supply chain. Processes such as Nonconforming Materials, Supplier Qualification, Supplier Review, etc.
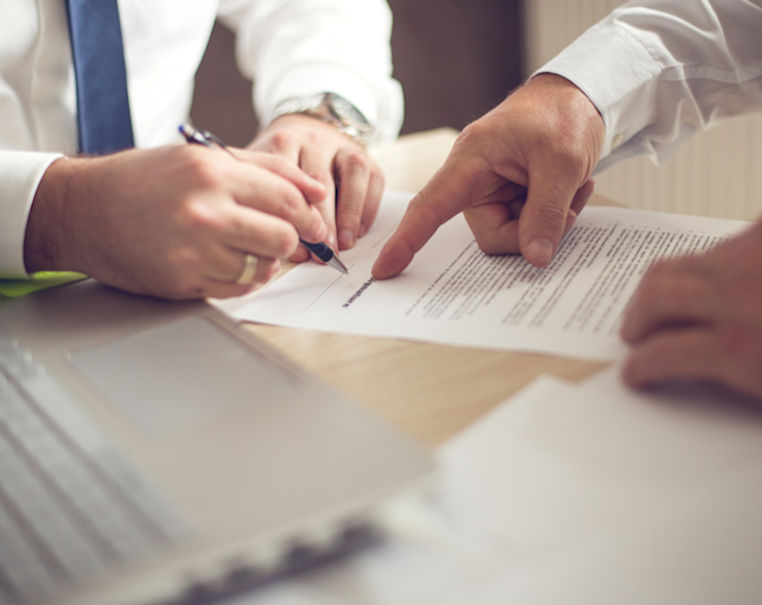
These are critical for the ability to meet demanding compliance and quality targets. In many companies, Quality and Regulatory Affairs reports directly to the head of Operations and hence have a direct say in effective margin generation. The quality strategy and the compliance processes set up at the beginning of a product creation process could have a substantial impact on the margins later on in the product’s life.
Executives in the company must have access to relevant process metrics and trends so that they can measure the effectiveness of their product commercialization activities. They need to be creative and efficient while, in many cases, maintaining compliance with various regulatory standards (e.g. RoHS, WEEE, FDA, ISO).
Critical areas for Quality Management and Regulatory Affairs departments are:
- Tracking of design control activities, product structure, changes and synchronization of product information e.g. product requirements, design specifications, assembly procedures, manufacturing instructions, compliance etc.
- Effective management of Company’s Quality processes (e.g. Corrective Action and Preventive Action, Complaint Management, Nonconforming Materials Management, Supplier Qualification and review etc.)
- Managing Compliance records, submissions and processes
QuadRite’s RitePro™ solution provides a built-in, best practice based information model, business rules and use cases to address the above-mentioned concerns for the document control group as well as facilitating the requirements of the other departments in the enterprise.
RitePro is an out-of-the-box application that can be deployed within days, instead of months. As a fully web-native application that is offered as a cloud-based or in-house solution, it minimizes the IT support need and enables ease of information access and sharing across the extended enterprise.