Engineering teams across the enterprises are being asked to focus on design for operational excellence since 70%-80% of the product’s operations costs are determined by the choices made by the engineering department during the design process.
A critical element for the overall success of commercializing a product profitably entails having strong and effective collaboration between Design Engineering, Manufacturing, Procurement and Product Engineering from the very inception of the product development activities and enabling the Design Engineering Team to use supply chain information early in the product design activities.
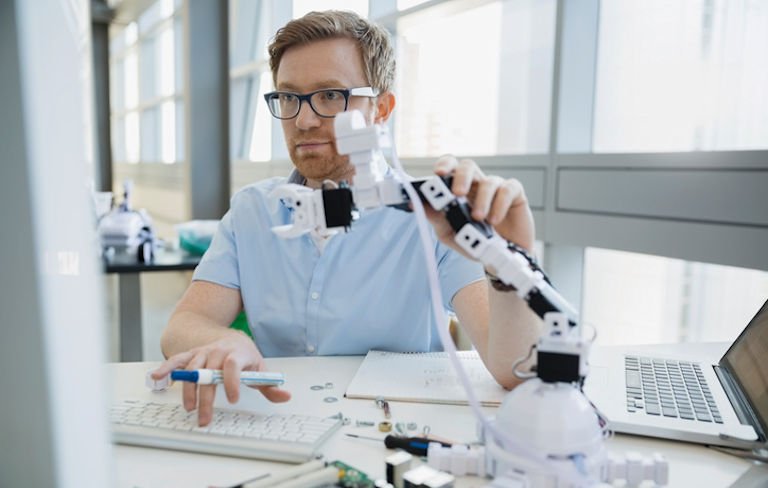
To effectively manage this type of operationally focused product development an enterprise needs effective Design Control, Document Control, and Engineering Change processes. In addition, Engineering must have efficient management of processes that expands beyond the company’s boundaries into the entire supply chain. Processes such as Supplier Qualification, First Article etc., are critical for the ability to meet demanding margin targets. Executives in Engineering must have access to relevant process metrics and trends so that they can keep their fingers on the effectiveness of their product engineering activities. They need to be creative and efficient while, in many cases, maintaining compliance with various regulatory standards (e.g. RoHS, WEEE, FDA, ISO).
As part of the overall strategy and the efficient use of capital challenge that companies are facing, more and more companies are focusing on specific core competencies and partnering for product design and manufacturing with other companies. This environment is creating a strong need for sharing of accurate product information both within the enterprise as well as throughout the supply chain.
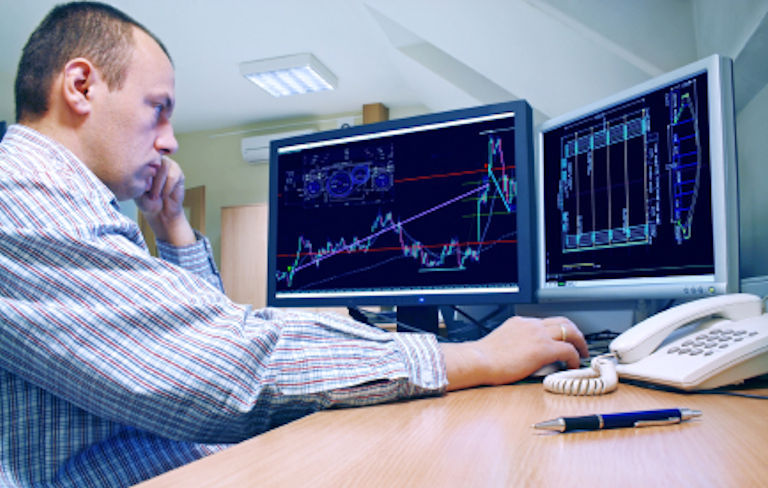
Critical areas for Engineering during the product development process are:
- Tracking of design revisions, product structure changes and synchronization of product information e.g. product requirements, design specifications, assembly procedures, manufacturing instructions, compliance, etc.
- Sharing of accurate information with design, engineering and manufacturing partners
- Managing the Life Cycle of products and configurations
- Managing Engineering Change Processes
- Accessing and incorporating supply chain information into the product development processes
QuadRite’s RitePro™ solution provides a built-in, best practice based information model, business rules and use cases to address the above-mentioned concerns for the Engineering group as well as facilitating the requirements of the other departments in the enterprise.
RitePro is an out-of-the-box application that can be deployed within days, instead of months. As a fully web-native application that is offered as a cloud-based or in-house solution, it minimizes the IT support need and enables ease of information access and sharing across the extended enterprise.